Core Substrates
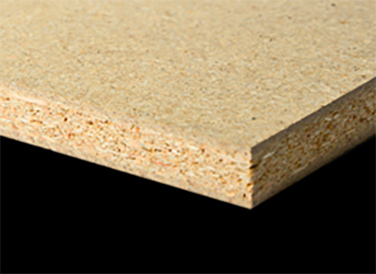
Particleboard
Particleboard, the standard wood core for our laminate countertops, is expertly crafted from high-quality wood by-products sourced from sawmills and wood processing facilities. This eco- and budget-friendly alternative to solid wood panels is perfect to enhance your interior projects.
Countertop manufacturers use particleboard in a variety of sizes, but generally ¾” thick panels in 30″ widths in 8’, 10’ and 12’ lengths are most suitable for countertop cores. Unfinished particleboard’s smooth, consistent surface is ideal for lamination.
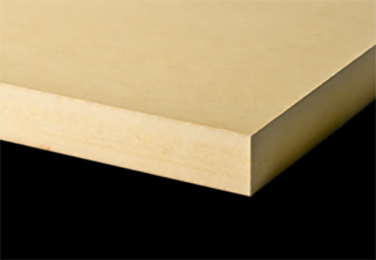
MDF
Medium Density Fiberboard (MDF) is a high-quality composite wood product, similar to particleboard, created by bonding wood fiber by-products with resin under heat and pressure. Its smooth, uniform surface and resistance to warping make it an ideal choice for various applications, including countertops, cabinetry, and molding.
MDF excels in high-humidity environments such as kitchens and bathrooms due to its excellent moisture resistance, which minimizes the risk of warping or swelling. Additionally, its low “tear out” ensures a smooth, clean cut when sawed, enhancing the quality of the finished product.
Builders and fabricators appreciate MDF for its versatility in applications ranging from laminate countertops and furniture to shelving, laminate flooring, decorative molding, and doors. It is valued for its insulating properties in sound and heat and can be easily nailed, glued, screwed, stapled, or attached with dowels.
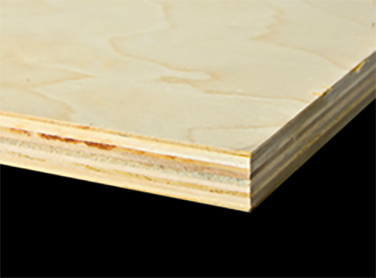
Plywood
Plywood is a robust wood product composed of multiple layers of veneer, or plies, bonded together with their grains oriented in alternating directions. This construction provides plywood with exceptional strength and adaptability, allowing it to be treated in various ways based on its intended use. It is capable of resisting cracking, bending, warping, and shrinkage, depending on its thickness.
Available in different types, plywood can be made from softwoods or hardwoods to suit specific applications. Softwood plywood, typically made from pine, fir, or spruce, is light in color and commonly used in construction. For decorative purposes, plywood may feature a veneer of exotic hardwoods. Aircraft plywood, known for its exceptional strength, is often crafted from mahogany or birch.
For countertop applications, plywood is generally produced in a thickness of ¾” (23/32”), with a 7-ply construction, and available in dimensions of 30” by 8’, 10’, and 12’ lengths. In some cases, plywood cores for countertops are specified requirements for HUD installations.